Rubber Crosslinking
Organic peroxides are used as crosslinking agents of variety of polymers. A crosslinked polymer shows improved properties compared to the uncured one:
- Reduced deformation under compression
- Improved elastic properties (elongation)
- Improved heat resistance (ageing, creep)
- Improved chemical resistance
- Increased abrasion resistance
- Improved resistance to stress cracking
Formulated Grades
Arkema provides the organic peroxides as technically pure grades, solid or liquid, and as formulated grades in selected binder.
Technically pure peroxides may be available as liquids at room temperature or as low melting point solids. They are especially used in cable applications.
For the crosslinking of elastomers, formulated grades are preferred. In fact, a formulated organic peroxide provides specific benefits, when compared to a technically pure one:
- Improved easiness of mixing in the rubber compound
- Improved handling
- Improved safety
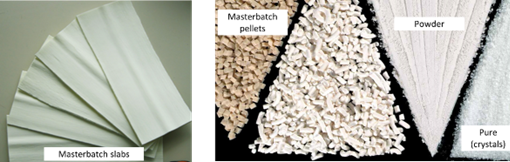
Technically pure peroxides may be available as liquids at room temperature or as low melting point solids. They are especially used in cable applications.
For the crosslinking of elastomers, formulated grades are preferred. In fact, a formulated organic peroxide provides specific benefits, when compared to a technically pure one:
- Improved easiness of mixing in the rubber compound
- Improved handling
- Improved safety
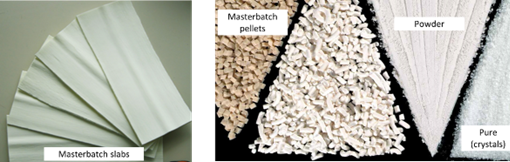
Masterbatches: contain 40% of active peroxide thoroughly dispersed in polymers (EPM typically) and fillers (CaCO3 and Silica). Available both in pellets and slabs, the physical form of masterbatch provides the highest quality of dispersion in the rubber compound with reduced mixing time. These masterbatches are essentially pre-compounded peroxide in elastomer and provide the benefits of creating final crosslinked parts with consistent physical properties that meet design specifications.
Granules: contain 40% or 45% of active peroxide, mixed in inert fillers (CaCO3 or surface treated kaolin clay) and compacted in cylindrical granules. They are easy to handle and mixed in the rubber compound. Granules can be used both in internal mixers or open mills.
Powders: contain 40% or 45% of active peroxide, mixed in inert fillers (CaCO3 or surface treated kaolin clay). Powders are best for use in internal mixers.
The choice of the most adapted grade depends mainly on the selected compounding technology and production parameters.
Granules: contain 40% or 45% of active peroxide, mixed in inert fillers (CaCO3 or surface treated kaolin clay) and compacted in cylindrical granules. They are easy to handle and mixed in the rubber compound. Granules can be used both in internal mixers or open mills.
Powders: contain 40% or 45% of active peroxide, mixed in inert fillers (CaCO3 or surface treated kaolin clay). Powders are best for use in internal mixers.
The choice of the most adapted grade depends mainly on the selected compounding technology and production parameters.
MIXING TECHNOLOGIES |
MASTERBATCHES SLABS |
MASTERBATCHES PELLETS |
GRANULES |
POWDERS |
PURE GRADES (LIQUID / MOLTEN) |
Internal mixer or continous compounder | ●●● | ●●● | ●● | ●● | |
Open mill | ●●● | ●● | ● | ||
Blending with polymer pellets | ●● | ● | ●●● | ||
Continuous feed in extruder's hopper | ●●● | ● | ●● | ||
Direct peroxide injection in extruder | ●●● |